Industrial control systems are control systems and associated instruments – devices, systems, networks, and controllers – used to operate and automate industrial processes. They vary depending on the industry they are used in. The differences include functions, task management, and build.
The industrial control systems can be divided into several classes, depending on their control action’s relative complexity of the overall function. The two most commonly applied types of these systems are Supervisory Control and Data Acquisition (SCADA), and Distributed Control System (DCS).
Supervisory Control and Data Acquisition (SCADA)
Supervisory Control and Data Acquisition provides control at the supervisory level. It does not offer full control. SCADA systems can be composed of devices situated in several locations. They are integrated with a Human Machine Interface (HMI), which provides centralized monitoring, as well as numerous process inputs and outputs. This type of industrial control system can be used to acquire and transmit data.
Distributed Control System (DCS)
Distributed Control System is used to control production systems situated in one location. In this type of industrial control system the set value is sent to the actuator, or the controller with the ability to instruct valves, in order to maintain operations necessary to sustain the required set point. DCS stores the data from the field. It can later be used for simple process control, as well as advanced control strategies.
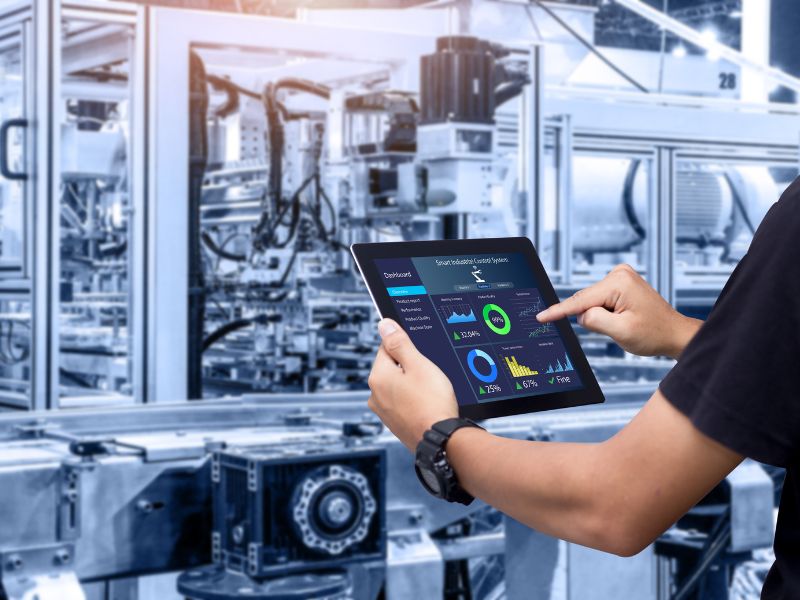
The role of the industrial control systems
The role of the industrial control system depends on the type of said system.
The role of the Supervisory Control and Data Acquisition
The Supervisory Control and Data Acquisition (SCADA) is used mostly for long distance monitoring and control of field sites through a centralized control system. It can automate the task and gather data in place of the workers, preventing them from having to travel long distances. This type of the industrial control system can control local operations such as:
- opening and closing of valves and breakers,
- collecting data from the sensor systems,
- monitoring the local environment for alarm conditions.
The role of the Distributed Control System
The Distributed Control System (DCS) manages multiple local controllers or devices that are part of the overall production process, using a centralized supervisory control loop. It allows the industries to quickly access both production and operation data. DCS can be also used to reduce an impact of a single fault on overall system, which is possible due to the exploitation of multiple devices within the production process.
Where the industrial control systems are used?
Different sorts of industrial control systems electronic applications were used in time by various industries. Currently these systems are being applied in nearly every industrial sector, critical infrastructure, and areas of industrial production, such as:
- manufacturing,
- chemical manufacturing,
- transportation,
- electric power generation,
- oil refineries,
- water and wastewater treatment.
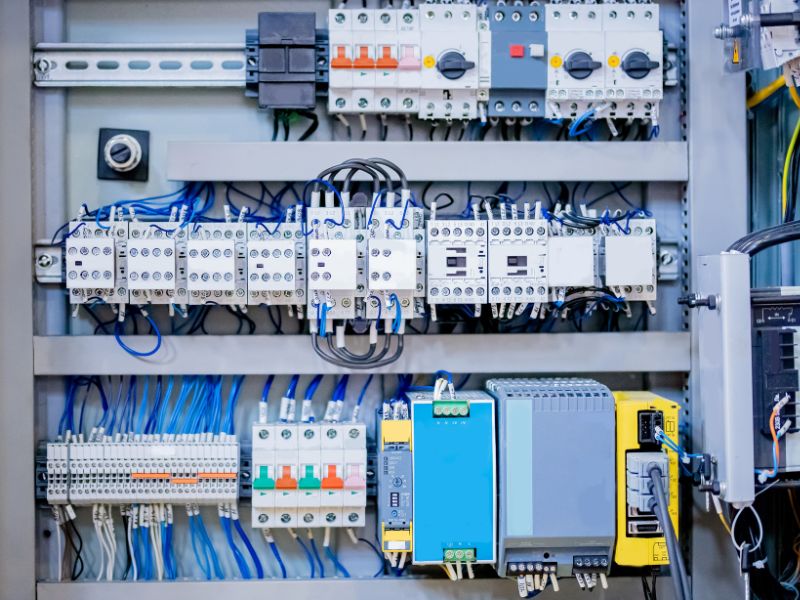
How industrial control systems can increase production efficiency?
Industrial control systems can significantly improve the business by enhancing productivity both on the plant floor and in other areas. They speed up production time, which leads to the optimization of the distribution channels and processes. By doing so, these systems help increase the sales, as well as customer service operations. As a result, the correctly implemented industrial control systems can greatly increase not only production efficiency, but the business operations in general.
Control systems manufacturer CS-Lab offers the best industrial control systems which can be used to increase production efficiency of a company and prove beneficial to its overall operations.